A Dentist’s Guide to Craft 3D Printed Dentures in a Lab
Dentures have been around for a long time, but since 3D printing has become more common, their popularity has grown more than ever. 3D-printed dentures are more comfortable and natural-looking than conventional approaches.
The advantages of printed dentures for dentists include the elimination of expensive and cumbersome impression materials. The option to order a 3D mock-up for try-in also reduces chair time and necessary adjustments after the initial fitting.
Moreover, 3D printing has made it possible to make dentures that are much more tailored to each person's mouth, and can bear many different colors and patterns.
Let's look closer at the process of printing 3D dentures to guide and inspire you to incorporate such technology in your dental lab:
1. Build Your 3D Virtual Denture Design
Utilizes a chairside scanner to obtain a three-dimensional image of the patient's anatomy. Store these photos in files for electronic transfer to the lab. Alternatively, you may send the denture lab physical impressions and a bite register.
You can use a CBCT scanner to scan alginates, stone models, and appliances and then import the resulting CBCT DICOM–STL files into various software programs for 3D printing. Through sophisticated CAD/CAM software, you can build nearly entire dentures.
2. Establish Production Parameters
Given that denture baseplates are a shade of pink and denture teeth are created from a tooth-colored material selected by the physician, baseplates and denture teeth are printed in two separate passes during the same production process.
Upper and lower virtual denture base pictures are oriented vertically using computer software to reduce the number of sprues or supports in the final product. The thickness of the finished baseplates is supposed to be constant throughout.
The software splits the baseplates into thin segments, and thinner slices improve denture fit. Although dentures made from thinner slices are of higher quality, the amount of time required to manufacture them increases tremendously.
So, slice thickness and time are balanced to make dentures quickly. Upper and lower baseplates can usually be printed simultaneously in a time frame of 1 to 2 hours. Printing the matching teeth also takes about the same amount of time.
3. Print the Dentures with Your Chosen 3D Printer
After the production parameters have been established, the printer build plate is dipped into a container of liquid polymethylmethacrylate resin, and the incremental build process commences.
The 3D Printer employs UV light to gradually solidify resin until the virtual design is transformed into an actual object. A metal scraper is used to remove the cured denture baseplates after the supports are left on the denture baseplates.
4. Conduct Post-Manufacturing Cleaning
The unbroken baseplates and their supports are transferred to a solution of isopropyl alcohol to eliminate additional alcohols produced during the printing process. The entire bath is placed for 5 minutes in an ultrasonic unit and repeated with a fresh bath of isopropyl alcohol.
After manufacturing, the remaining sprue connections are sanded with a Scotch Brite wheel mounted on a rotating handpiece. Set the baseplates aside and repeat steps 3 to 5 to create tooth-colored baseplates and precise-fitting teeth. Like baseplates, upper and lower arch teeth are produced simultaneously as a single unit.
5. Merge Components
Each tooth socket within the baseplates is filled with liquid baseplate resin by a denture specialist. Then, the teeth are inserted into the sockets, with their supports intact. The gaps between the teeth and the baseplate are filled with liquid resin using a tiny brush.
Both dental prostheses are put in UV curing equipment for 30 seconds to bond the teeth to their respective baseplates. On the teeth, the sprues are eliminated. Once more, a Scotch Brite wheel is utilized to eliminate extra support material.
6. Curing the Resin and Finishing the Polish
Understanding how to clean and polish an object after taking it out of a 3D printer is a crucial component of the process. Before being handled or utilized intraorally, the print must be cleaned in an alcohol solution, dried, and UV-cured. Moreover, many 3D printer manufacturers include post-processing and wash stations.
Conclusion
Dentures made with a 3D printer are an interesting example of a new technology changing how dentures are made. Integrating 3D printing of dentures in your dental clinic benefits your patients and your bottom line. Your investment will streamline operations, lessen the time needed to create dentures, and help you improve patient satisfaction.
For quality
3D printed dentures, Vitality Technologies offers a new digital denture material system and workflow to improve strength, aesthetics, and lab efficiency. We partner with digital dental labs and offices throughout the country. If you're ready to supply 3D Digital Dentures, partner with us today! Get a free introductory call with our lab technicians and discover the benefits of going digital for your practice.
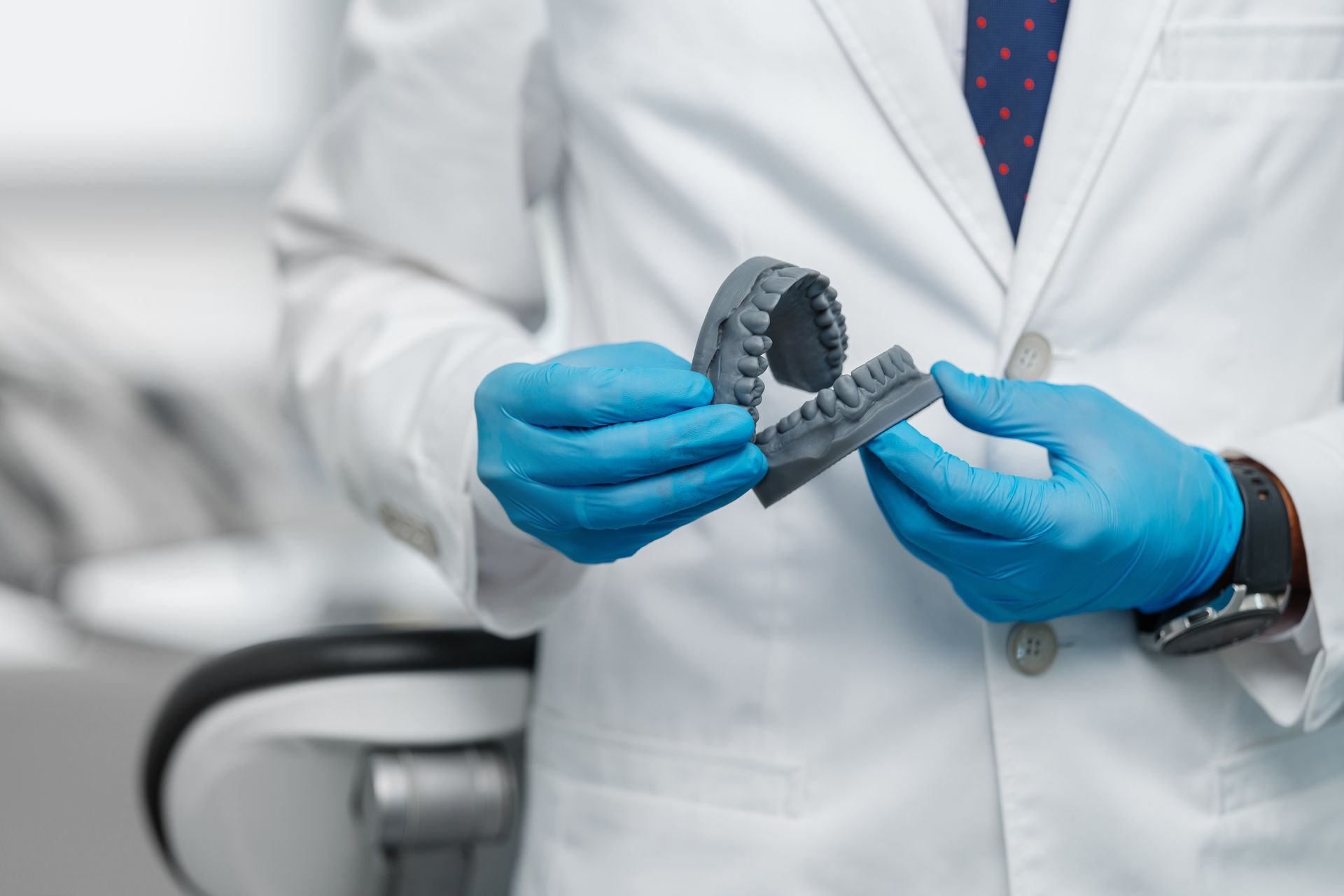
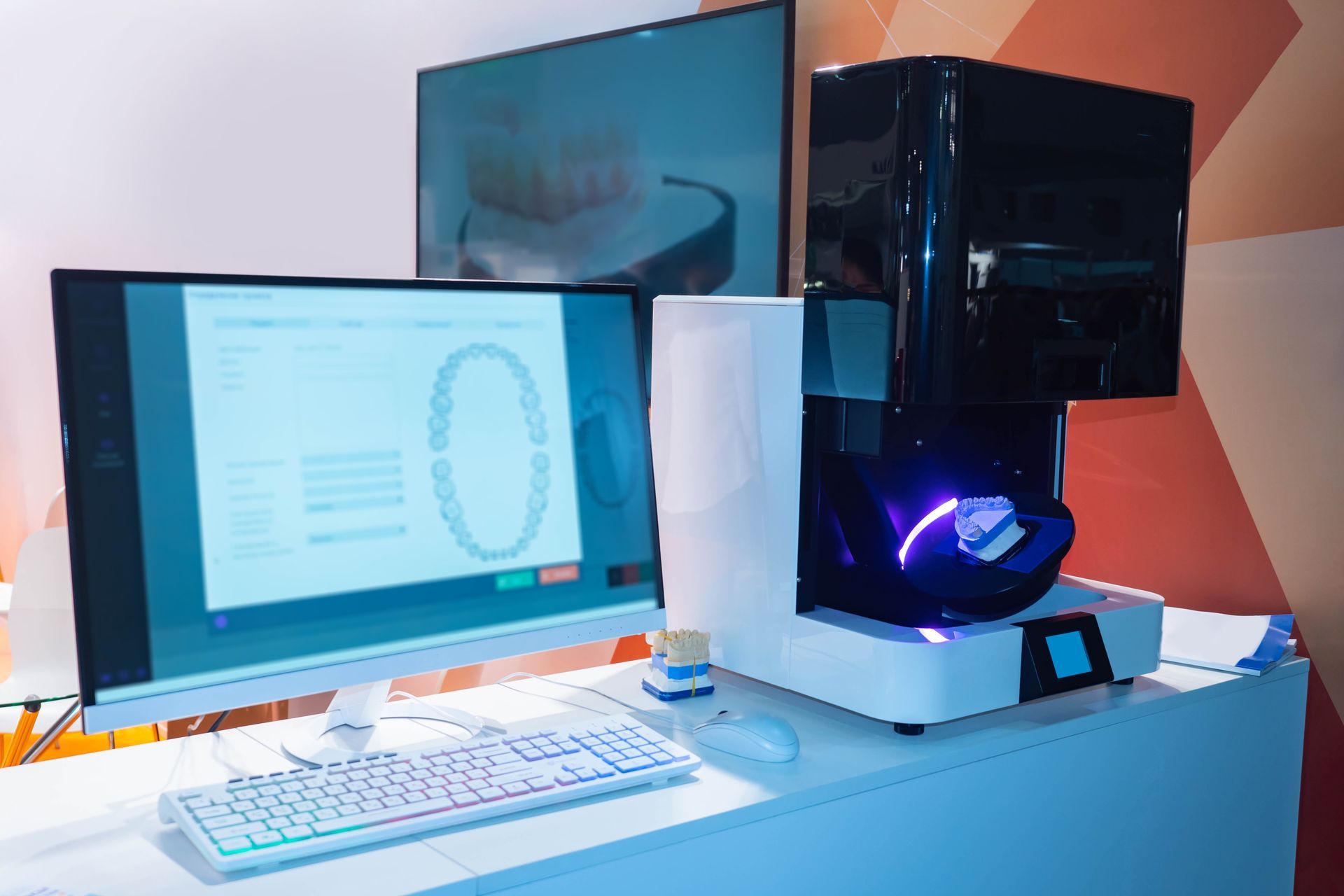
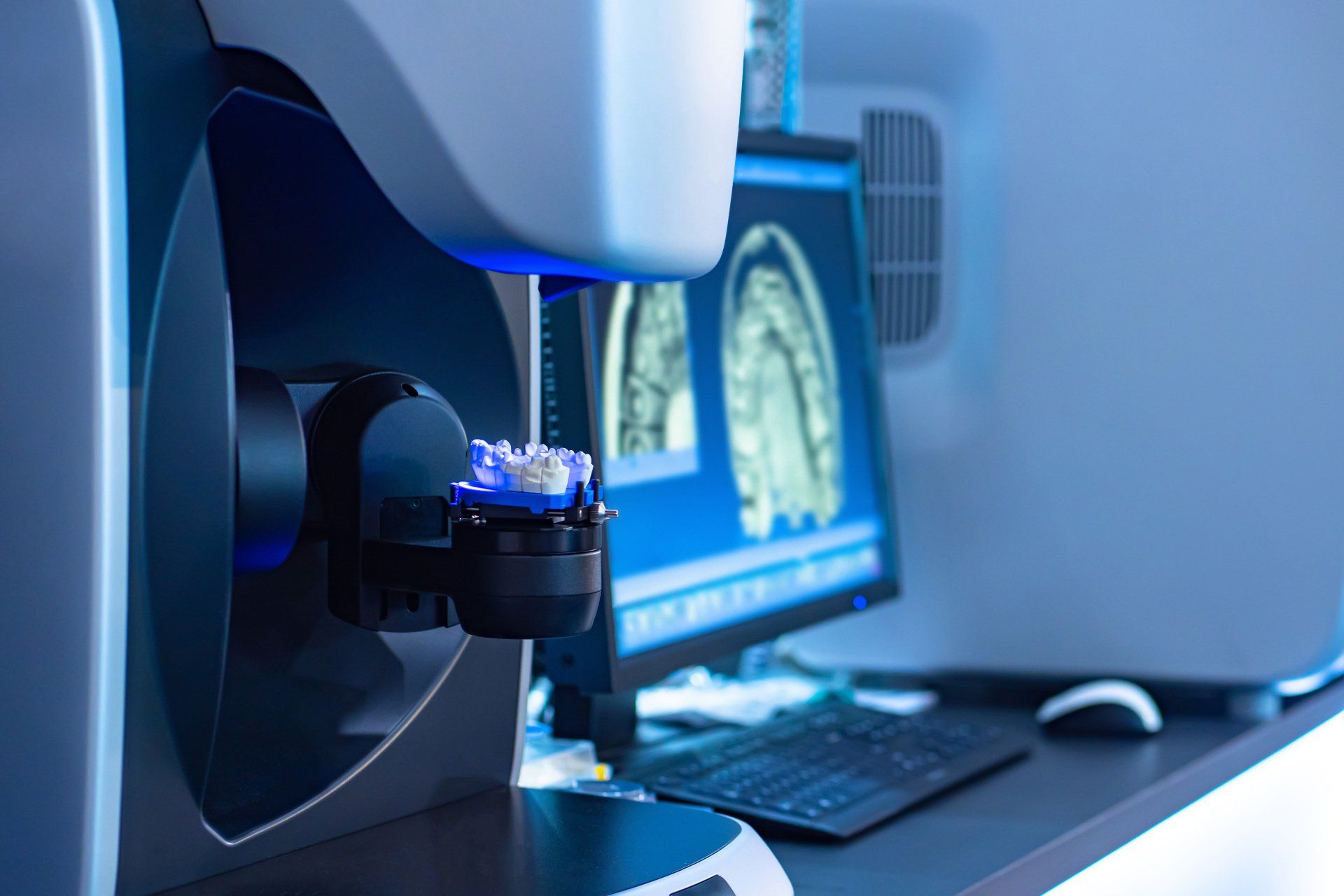
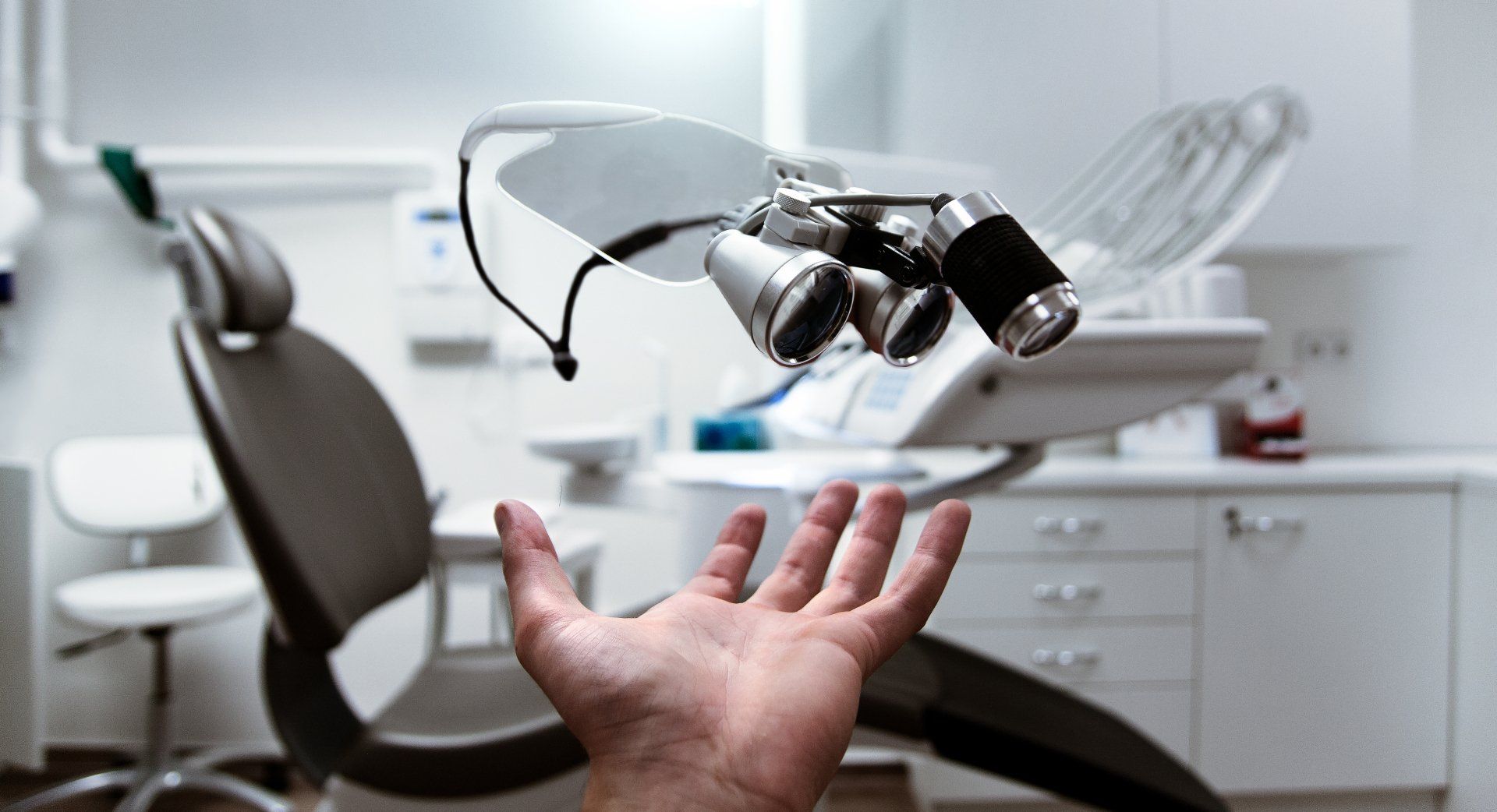